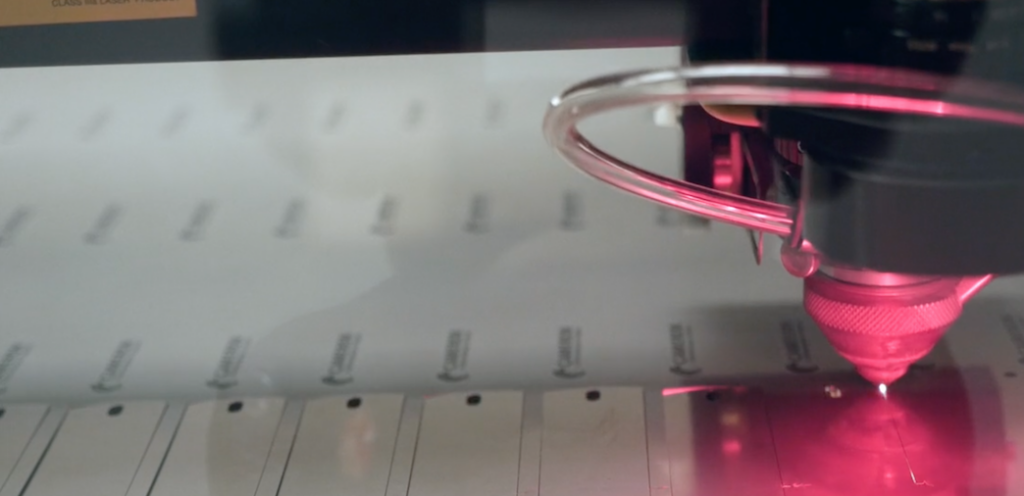
Industrial nameplates are crucial for many industries. Custom etched or engraved nameplates allow you to communicate important information including variable data, and contribute to the accuracy and efficiency of your operations. At Etched, we create high-quality nameplates customized to your exact specifications, using durable materials that will resist corrosion and last for years, even in harsh industrial environments. In this buyer’s guide, our experts will walk through your options for specifying an industrial nameplate, and which material and process type might be best for your application.
How to select a material type for your industrial nameplate
At Etched, we can manufacture industrial nameplates using stainless steel, aluminum, anodized aluminum, or plastic. Each material type has its own advantages and disadvantages, and is best suited for different applications.
Stainless steel industrial nameplates
Stainless steel is the most durable option for nameplates. An etched stainless steel plate will remain clearly readable for as long as the material will last in your environment, and stainless steel is the substrate best suited for withstanding the elements and resisting corrosion and abrasion. If your nameplate will be installed in a coastal area or environment with significant salt spray, or if it will get transported often across worksites or in the backs of trucks, stainless steel may be the best option.
At Etched, we stock stainless steel in 0.018” – 0.125” thicknesses. Both 316 and 304 stainless steel are available in most thicknesses. When ordering, you can also specify the finish option. The #4 finish contributes a shinier exterior to your nameplate, whereas the #2B has a matte/duller finish.
Aluminum industrial nameplates
Like stainless steel, aluminum nameplates will last a long time even in harsh industrial environments. However, they are less resistant to corrosion, and are better suited for indoor applications or environments without extreme or abrasive conditions.
Aluminum nameplates are the most common choice for the aerospace and transportation industries, or any application where weight is at a premium, since aluminum is significantly lighter than stainless steel. At Etched, we stock aluminum in 0.012” – 0.125” thicknesses, with other thicknesses available upon request.
Anodized aluminum industrial nameplates
Anodization is the process of applying a protective coating to a raw aluminum substrate, providing additional abrasion resistance and protecting the material against corrosion and the elements. Featuring the same light weight as raw aluminum, but with enhanced durability, anodized aluminum is well-suited for indoor or outdoor applications where weight is at a premium.
When ordering, you can specify the color of anodized aluminum, including clear, black, blue, green, red, or yellow.
Plastic industrial nameplates
Plastic is the least durable substrate for industrial nameplates, meaning it is best suited for indoor applications or environments without direct sunlight or the need for extreme rigidity. However, plastic offers the highest contrast when text is engraved on a different color background, lending plastic nameplates enhanced legibility.
How to select a process type for your industrial nameplate
At Etched, we offer an array of etching and engraving services to produce the best solution for communicating valuable information in a durable and lasting way. In this section, we’ll explain how each process works and the advantages and disadvantages of each.
Chemically etched nameplates
Chemically etched nameplates are manufactured by masking parts of the substrate with an acid resistant material. This allows the unmasked area to be dissolved away with acid, leaving the masked areas in relief. Chemical etching can be applied to stainless steel, aluminum, or anodized aluminum nameplates–but not plastic. The depth of the etch can vary from 0.0015 to 0.004 inches, depending on the design and the material used.
Chemical etching is the most durable and long lasting process option, and is highly resistant to abrasion. If you want your nameplate to be clearly legible for the entire lifetime of the substrate, chemical etching may be the best choice.
Metalphoto nameplates
Metalphoto processing permanently seals a UV-stable image inside anodized aluminum. The process works similarly to old-fashioned film photography development–we take a “negative” image and expose it on special aluminum, then process that material in a developer solution. Finally, the metalphoto is sealed in a glass-clear, sapphire-hard anodized layer that is highly resistant to chemicals, paint, abrasion, and dirt. The image created on the nameplate can last for over twenty years and is UV-stable, meaning even intense and direct sunlight won’t affect it.
Metalphoto is the most common choice for the military and aerospace industries, due to the highly durable, legible, and yet lightweight nature of metalphoto aluminum nameplates.
Laser engraved nameplates
At Etched, we have both fiber and CO2 lasers that are ideal for durable metal marking applications. The fiber laser creates a very durable image with a lot of depth, making it well-suited for nameplates that require a high contrast. However, the color of the mark made by a fiber laser is dark brown rather than a true black. CO2 lasers can create true black marks, but achieve less depth, making the finished nameplate less resistant to abrasion.
Laser engraving can be selected as a process option for any of our material types, including stainless steel, aluminum, anodized aluminum, and plastic.
Rotary engraved nameplates
Rotary engraving uses a rotating cutting tool in a motorized spindle to create a groove in a substrate at a specified depth. Etched uses an engraving bit to cut an average of 0.003 to 0.007 inches into the material. Engraved letters and graphics can then be filled with paint for greater contrast.
Rotary engraved nameplates are extremely precise and repeatable, since the drill follows a toolpath defined using specialized manufacturing software, so rotary engraving is an excellent choice for high-volume orders. It is also highly durable and offers a strong color contrast. Rotary engraving can be selected as a process option for any of our industrial nameplate substrate materials, including stainless steel, aluminum, anodized aluminum, and plastic.
Screen printed nameplates
Screen printing uses ink to create a crisp, clear, and durable image on your nameplate. Although the image is less durable and long-lasting than etching or engraving, screen printing is a cost-effective process option, especially for indoor applications, and can be applied to any material type.
How to select an industrial nameplate supplier
It is essential to find an industrial nameplate partner that can get you the right solutions in the right quantities, right when you need them. At Etched, we understand that running out of nameplates or using illegible or unclear plates can significantly hinder precision and efficiency on your operations. That’s why we are committed to offering the highest-quality materials and service, regardless of the size of your order.
The nameplate supply chain is costly, time-consuming, and riddled with inefficiencies for most companies. Be sure to partner with a supplier that offers unique supply chain solutions to ensure that you never have to worry about your nameplates again.
Here are a few questions you should ask your nameplate supplier before ordering:
- What are your minimum and maximum order quantities?
- What is your standard lead time for orders? Do you have options for rush orders or expedited shipping?
- What materials do you use for your industrial nameplates, and how do you ensure that those materials are high-quality and long-lasting?
- Do you have any processes in place to make reordering nameplates quick and easy?
- Do you manufacture your nameplates in the United States?
We’re here to help
Still not sure which material or process option is right for your application? Our team of industrial nameplate experts would love to help. Get in touch with us today!